"Pathfinder" Solution
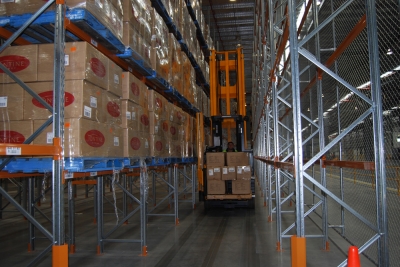
Jungheinrich's Warehouse Navigation technology is now being utilised in the distribution warehouse of Pacific Brands, in Victoria. Thanks to this "pathfinder" solution, narrow-aisle stackers and vertical order pickers are automatically guided to the right storage location, resulting in significant time savings and energy conservation.
Performance and Efficiency Increase with the Jungheinrich fleet.
The Pacific Brands Distribution Center, equipped with all new Jungheinrich EKX5 series turret stackers, and EKS3 series vertical order pickers, was commissioned in early 2013. Pacific Brands had a great amount of business consolidation and process implementation to establish in the new facility, and after some months of bedding in, the Jungheinrich ‘Warehouse Navigation and automatic rack approach technology’ already on-board the order picker/trilateral stackers, was switched on. “The results were virtually immediate with improved picking rates the most obvious”
RFID helps minimise the time input for driving and stacking.
The RFID Warehouse Navigation system is an intelligent forklift management package not emulated by any other supplier, which enables the stackers to communicate not only with the floor as before, but also with the Warehouse Management System, whose data flows directly into the forklift control systems. The interface used for this data transfer process is exclusive to Jungheinrich. The Jungheinrich Warehouse Navigation can interface with ‘any’ Warehouse Management System.
Stacking Instruction Transmitted via Wi-Fi
The warehouse management system has transmitted the stacking instruction via Wi-Fi to the logistics interface of the vehicle terminal, which has duly forwarded it to the control system of the EKX 515. When arriving automatically at the location a positioning light automatically turns on for the correct side of the racking and the operator simply scans in the barcode on the pallet or carton. The vehicle terminal then displays the product, quantity and pallet type
The System Guides the EKX 515 on the Shortest Route
The stacker operator then inputs an incremental stock management number, and the warehouse management system specifies the required stacking location, selected according to the “chaotic”, or dynamic, storage principle. The operator picks the pallet up with the swivel fork of the EKX 515, confirms the stacking instruction, and steers the vehicle into the appropriate aisle. The warehouse navigation system now automatically guides the EKX 5 on the shortest route, at the optimum speed and with minimum energy input, to the required location.
20 Percent Productivity Increase - The efficiency is further boosted by special diagonal speed profiles (lifting whilst driving)
Using a combination of the ‘floor topology’ and ‘RFID floor control’ modules, the speed profiles of a stackers can be adapted according to the floor conditions at various points in a narrow-aisle warehouse, for example for zones with poor floor quality or when working with fragile cargo. The vehicle control system operates on the basis of continuous travel distance measurements and aisle location transponders, which combine as a redundant system to provide an extremely high level of reliability, more accurate than a GPS.
Greater Flexibility Thanks to RFID Technology
The floor topology and consequent speed adjustments can be saved in the memory of a master vehicle and then transferred via a USB flash drive to each of the forklifts operating in the narrow-aisle areas. The RFID floor control system also provides even greater flexibility for the EKX 515 in terms of its switching and safety functions, including aisle end overrun protection and lift and driving cut-offs.
But over and above the benefits of the Warehouse Navigation system, the EKX 5 series also offers high productivity, dynamic movement response and lower energy consumption, thanks to its 80 volt, three-phase AC technology. The high torque of these vehicles results in powerful acceleration, fast lift and responsive ancillary movements. The EKS 3 series vertical order pickers offer the same performance skills and attributes.
Another feature is the ability to raise and lower the main and additional lift simultaneously. The efficiency of the EKX 5 series induction-powered stackers operated by Pacific Brands in its forty-plus narrow aisles, each approximately 90 metres long, is further boosted by special diagonal speed profiles defined according to travel direction and height.
Single Battery Charge Good for Two Shifts
At times of peak demand Pacific Brands needs its high-bay stackers, to handle several hundred stacking and retrieval movements a day. This is where the outstanding stamina of EKX 5 comes into play. Even when the vehicle has been constantly in use from early a.m. to late p.m., the two shifts can be completed on a single battery charge. This is due to extremely efficient AC energy and drive systems, the dual energy recovery process, from regenerative braking on the one hand, and lowering loads on the other, along with an active energy and battery management system, used to optimise energy flows in advance and avoid energy overload peaks.
Jungheinrich ranks among the world’s leading materials handling flow engineering sectors. The company is an intralogistics service and solution provider, with manufacturing operations, which offers its customers a comprehensive range of forklift trucks, logistics systems service and advice.
NTP Forklifts Australia is the official Partner to Jungheinrich in Australia. NTP Forklifts Australia is the importer and distributor of the Jungheinrich range, as well as the full after sales support and spare parts network provider for Jungheinrich.